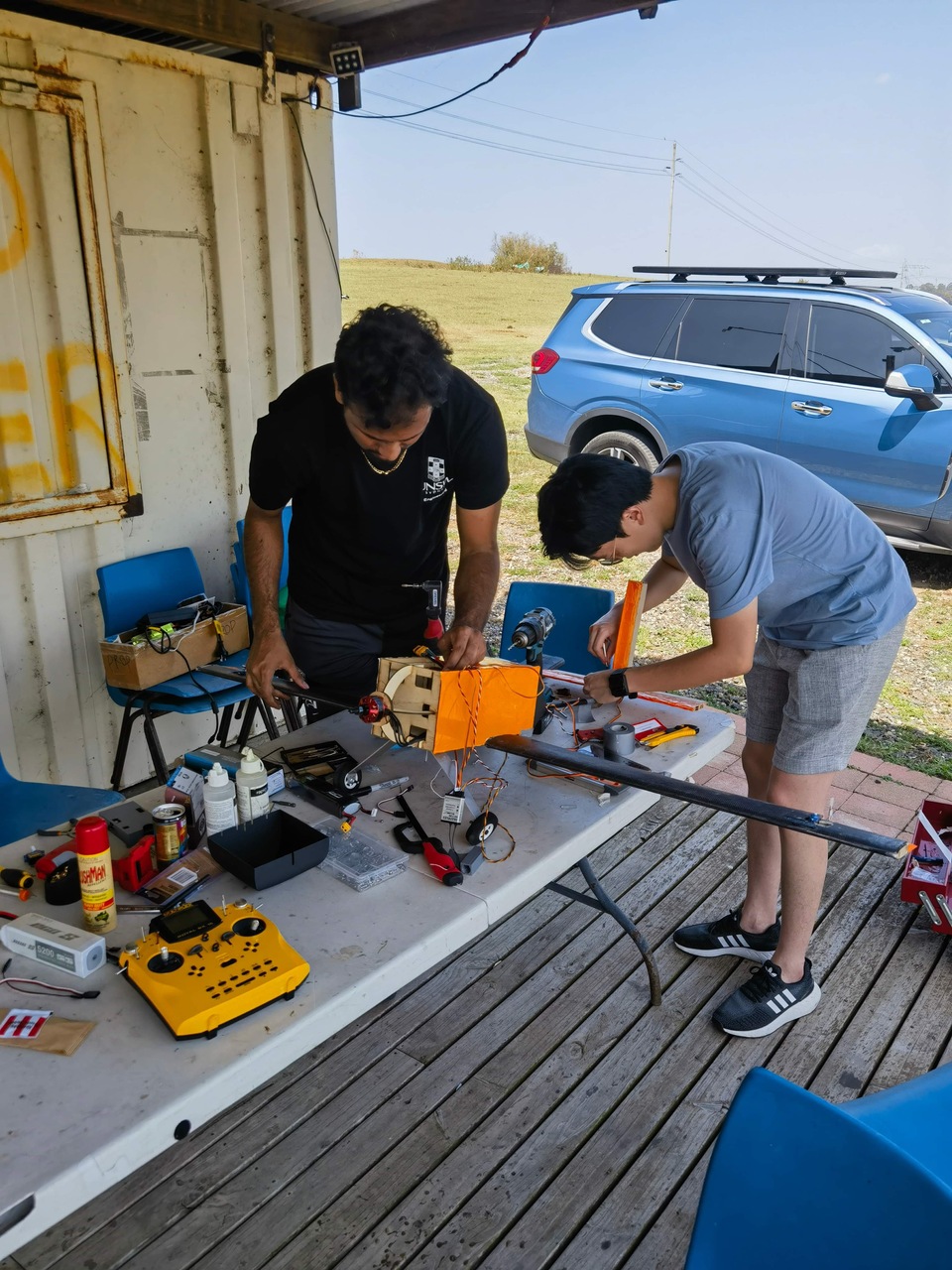
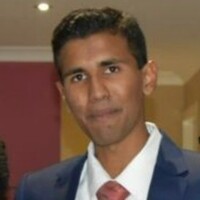
Akash Lakshman @alakshman1
Development of Prandtl D Wing (World's most efficient wing)
Development of Prandtl D Wing (World's most efficient wing)
Hi everyone,
I run an Aircraft Design Team at the University of New South Wales in Sydney, Australia and we've been hard at work on the development of the Prandtl D Wing based off NASA's flying wing design in 2016. In this case, it is utilised for a narrow body fuselage (first application that I've seen so far) with electric battery technology for long-range UAV's (2.8kg MTOW currently and possible upscale to 4.2kg). From all the development we have done, the maximized aerodynamic and structural efficiency compared to any other wing in the world is a great trade off for electric propulsion on small scale aircrafts as the large aspect ratio has virtually no practical limitations and the low thickness/chord ratio has no effect as the batteries are stored in the fuselage as opposed to many small petrol aircrafts that store fuel in the wings similar to jet aircrafts. Based off experimental testing and structural calculations, we utilised carbon fibre pre-preg for the wing skin and a carbon tube + wooden rib layout for the internal structure. This conservative option was essentially chosen over the idealistic design of a composite span-wise internal C beam and a torsion loaded wing skin due to practical concerns. This includes the manufacturing complexity and the build up of stress at the C intersection and the trailing edge due to sudden aerodynamic excitations. Fiberglass split moulds (based off foam plugs) were utilised to cure the pre-preg wing half skins in the oven and provided the jig alignment for the final composite joint bonding cures.
If it is not too much hassle, I'd love to hear from individuals in the composite community on where the development of this wing in this application (electric UAV, low MTOW) may be limited for wide-scale use. This will be great to help us set our focus as we proceed to refine the structural integrity and manufacturing quality for the next iteration.
Thank you for your time!